Advanced Automation with ROS 2 for Industrial Process Control Systems (PCS)
Human-machine collaboration has never called for as much flexibility and adaptability as in the era of Industry 4.0. Companies see Industry 4.0 as an opportunity to gain a competitive advantage to become market leaders or strengthen their market leadership.
However, more than half of companies surveyed by the German National Academy of Science and Engineering said they are lagging behind with digitalization. They explained this is mostly due to a lack of guidance and positive experience examples from industry leaders.
Our client—an innovative leading European food producer with manufacturing facilities across different countries—has been undergoing a digital transformation. The company wanted to move from reliable plants to smart plants equipped with a data-driven digital nerve system. This would enable faster and better decisions and, using advanced automation, allow plants to self-optimize at incredibly high levels.
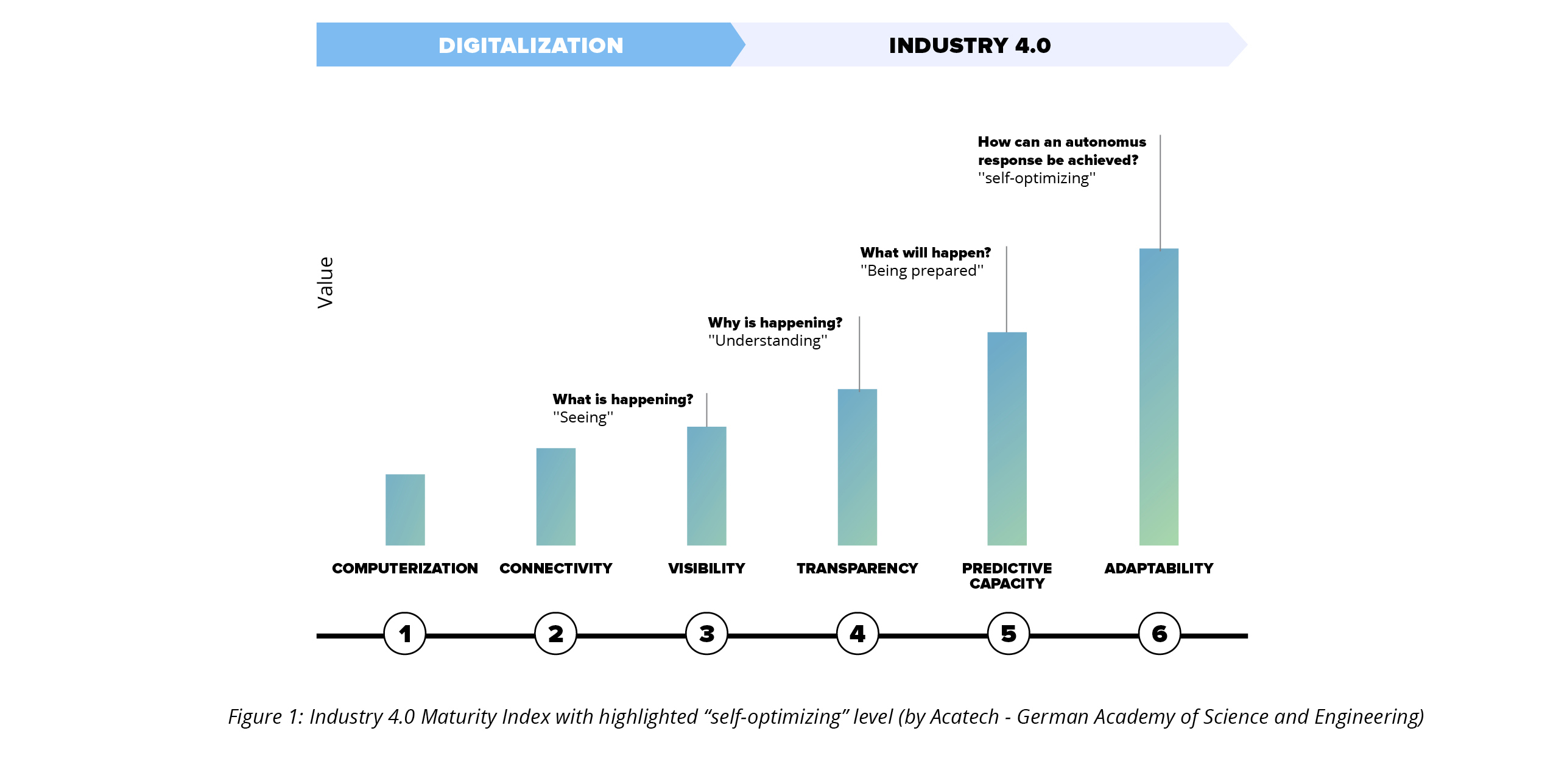
The main issues our client faced were:
- Conventional industrial controllers required frequent input from process operators as each machine’s controller was tuned individually. This forced skillful workers to tune low-level process variables instead of focusing on higher-level metrics.
- No centralized control of the factory to optimize its performance—each process/machine performance was optimized individually.
- A shortage of skillful workers in the industry and long onboarding time put significant pressure on the manufacturer. As a result, much effort was necessary considering personal experience with machinery.
- Lack of historical data storage for machine telemetry and operation data caused issues with handling similar manufacturing challenges over time or across different factories (for example, a year with low rainfall, or raw material quality changes).
- Significant challenges in optimizing industrial processes, due to lack of configuration options, difficulty adding new sensors, applying intelligent control algorithms, and simultaneously controlling multiple actuators.
- Seasonal changes in raw material quality caused frequent tuning of conventional industrial controllers by external vendors and led to operational cost increase.
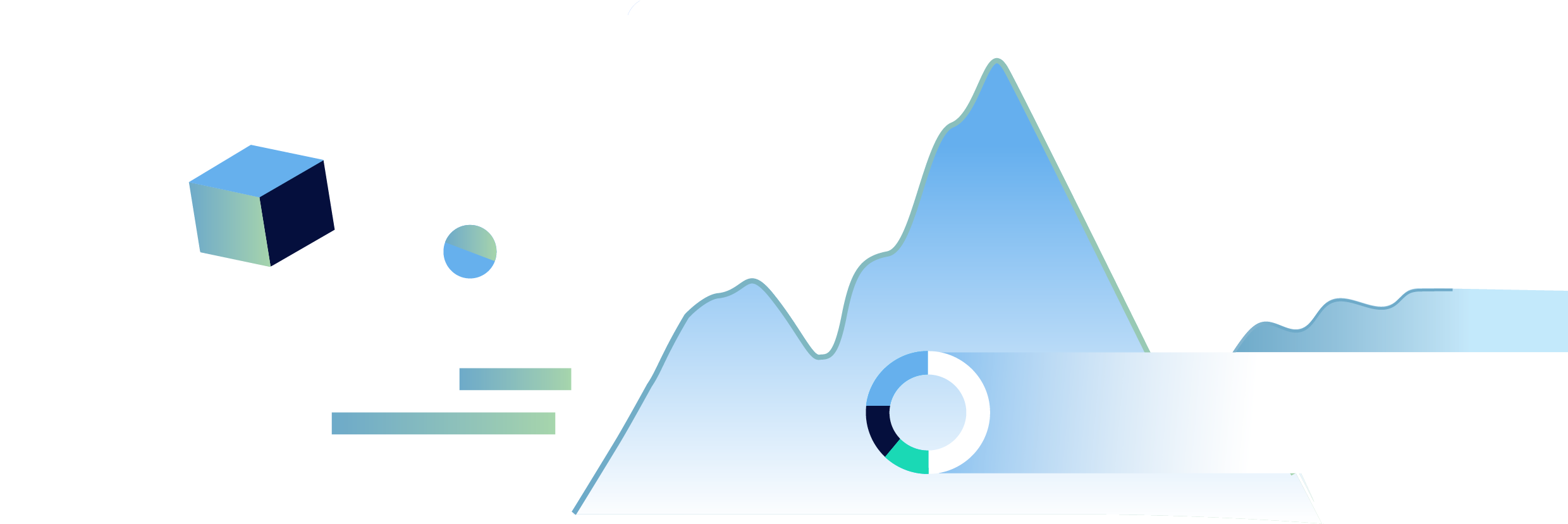
It was at this critical point that the client reached out to SoftServe for help, looking for a solution to transform their existing facilities into a smart digital factory.
Emerging technologies give an opportunity to solve old and difficult problems. In our case, the solution was ROS 2 (Robot Operation System version 2)—an open-source set of software libraries and tools created by a large community—including Amazon, Intel, Microsoft, Bosch, Toyota, and other influential industrial players.
Our client is also planning to utilize various kinds of autonomous robots at their factories. To help achieve this, and to make sure the solution stays compatible in the future, ROS 2 was selected as a middleware to run on industrial edge devices and in the cloud. Litmus was chosen as an edge platform.
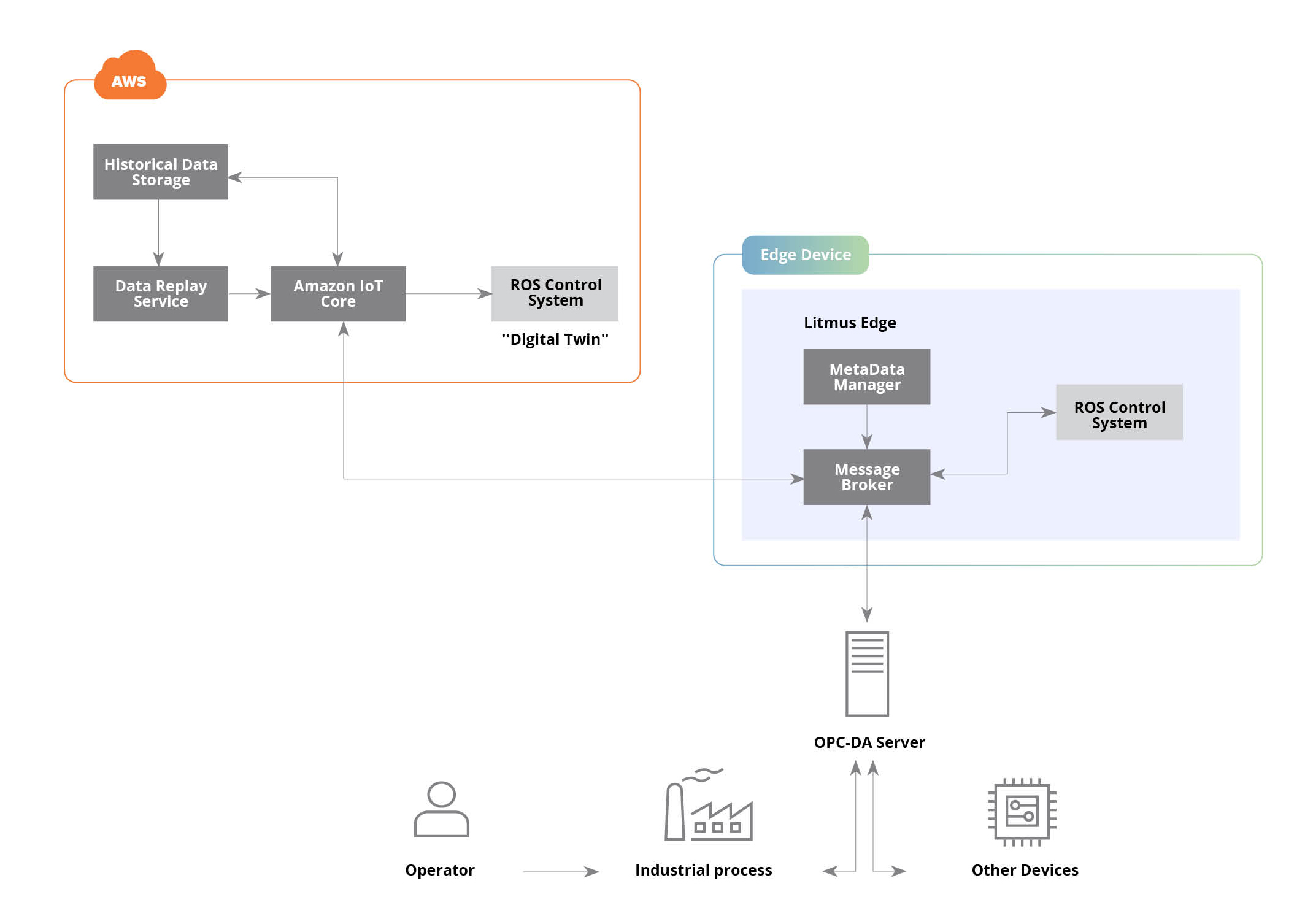
This is a pioneering concept of ROS 2 usage. The topology allows us to act on real-time data from a fleet of robots or industrial controllers, as well as to simulate different industrial processes on historical or synthesized data. This means treating all the factories as one ecosystem, consisting of multiple agents. Additionally, ROS 2 and SoftServe’s suggested approach allows for effective creation of a factory digital twin through a representation of physical assets and processes in the cloud.
SoftServe’s approach involved multiple stages starting from designing an architecture of the IoT Platform to implementing pioneering concepts with ROS 2.
Considering the importance of implementing smart factories, the Advanced Automation pilot project that SoftServe’s experts delivered to the client included:
- A ROS controller system that supports adding, evaluating, and managing new software controllers in a robust manner. This provides the flexibility, tuneability, and centralized manageability of algorithms that control industrial processes.
- Software SISO and MIMO controllers able to run in real-time.
- Enabling approaches that synthesize the process’ control outputs based on the readings from multiple existing and new sensors on various production stages.
- A solution that enables historical testing of various types of controllers, validating control algorithms on the historical data previously obtained in the production.
- A foundation for factory digital twin development.
- Infrastructure automation for both cloud and edge environments, supporting scaling according to customer needs.
A pilot project of this pioneering ROS 2 concept for industrial automation was conducted at one of the clients’ facilities with SoftServe experts’ remote support (due to COVID-19 restrictions). It demonstrated that ROS 2 can successfully take over functions of process control systems (PCS) by controlling a specific part of the production process.
Future Plans
The pilot phase showed the solution could successfully leverage ROS 2 for industrial advanced automation, and the full-fledged system coming next promises significant benefits for the business allowing to:
- Eliminate potential human errors
- Improve product manufacturing quality
- Increase the level of automation of industrial processes
- Reduce the cost of operation
LET’S TALK about how the SoftServe team can help you seize new opportunities and take your manufacturing quality and safety to the next level.