Build or Buy? Finding the Right Robotics Rig for Your Automated Inspection Needs
You know that effective inspection automation starts with the right robotics rig, and you’re not alone: Manufacturers deployed 5% more industrial robots worldwide in 2022, reaching a record of 3.9 million total units, according to the IFR. With a tight labor market and stiff competition for customers, there’s a strong impetus to save time by buying your robotics off the shelf. But that can saddle you with higher costs upfront and down the line.
The truth is that prefabricated robots never work right out of the box, so it will require time, effort, and resources to configure them. On top of that, ongoing supply chain issues mean that your robot may arrive later than you’d like. That’s all fine if the off-the-shelf robot checks all your boxes. But while it’s possible that there’s a robot on the market that perfectly fits your specifications, it's more likely that you’re overpaying for features you don't need.
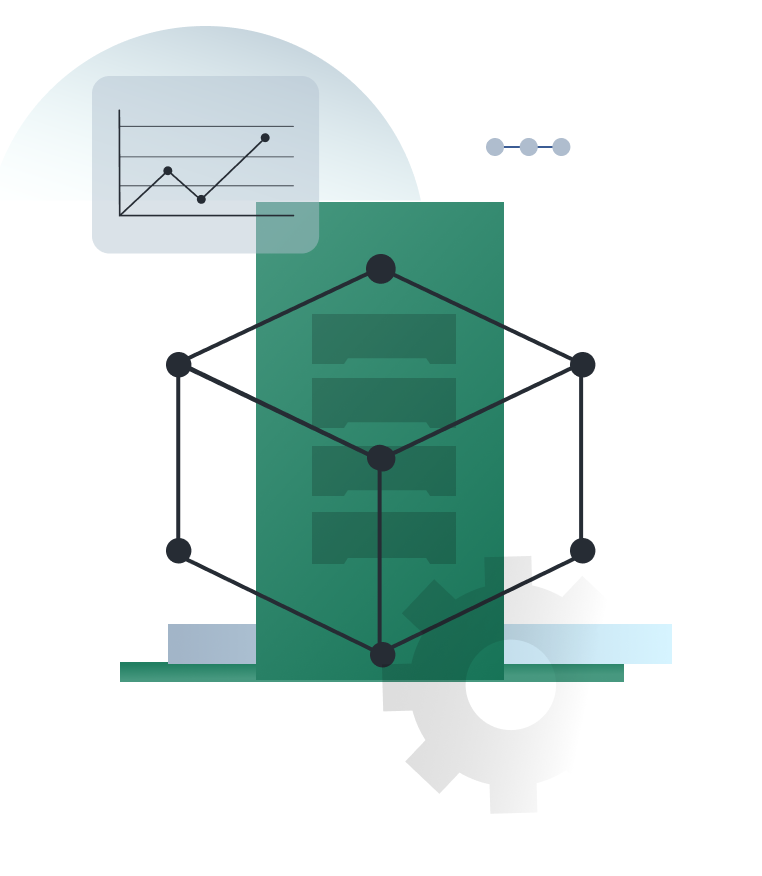
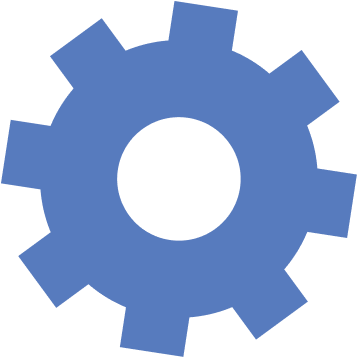
Arm, drone, or Spot? Don’t overpay for a robot with features you won’t use.
Automated inspections increase production speeds while reducing errors and shrinking reliance on manual labor. That’s why it might make sense to take the time to develop a custom robotics rig that perfectly fulfills your production needs. But to do that, you need to consider the operational parameters your automated inspect robot will need to function in — or risk catastrophic failure.
To help get you started, we’ve explained the importance of four essential considerations to make sure your robotics setup hits all the marks.
Will your robots need to operate outside?
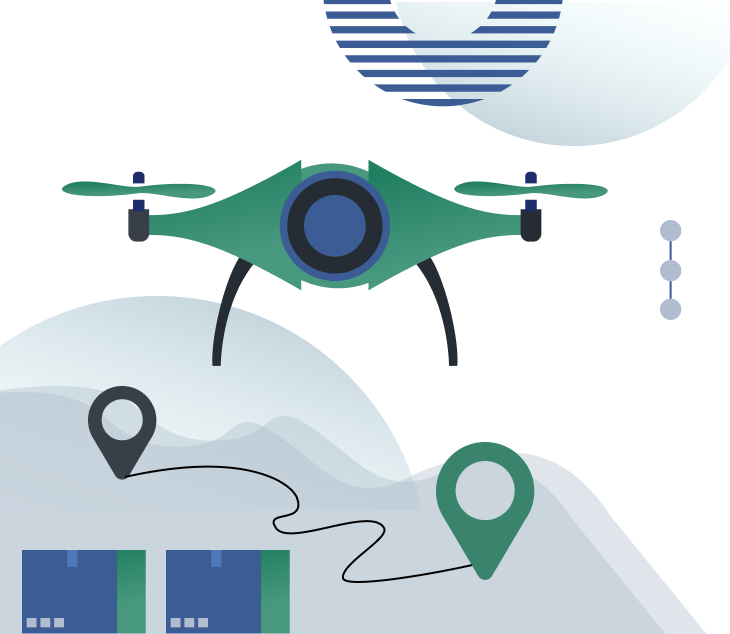
Specific design choices are necessary to make robots capable of operating in full exposure to the elements. Carrying out inspections underwater, for example, will require waterproofing, while working in muddy fields requires treads. Yet while waterproofing is merely superfluous for indoor work, the treads will destroy the concrete floor of an indoor production facility.
As a rule of thumb, outdoor robots need to be more robust, and that extra weight needs to be compensated for with more powerful motors. That means relying on bigger, more powerful batteries. But those batteries become unreliable at –10°C and must be thoroughly insulated.
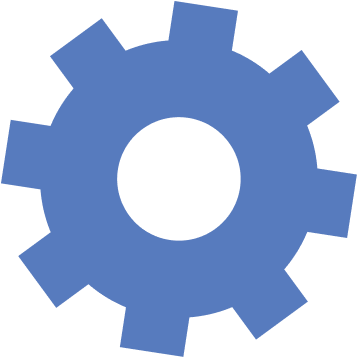
Outdoor inspections require more robust robots — using them indoors can damage your facility.
Moreover, charging batteries outdoors requires additional infrastructure. Pattern charging is a common method but necessitates that the robot can interact with perimeters. And every outdoor robot, particularly drones, should make use of either electronic perimeters, GPS, or RTK-GPS for localization. After all, you wouldn't want your crop inspection robot rolling into your neighbor’s field or simply disappearing over the horizon.
How will your robot navigate within the production environment?

At the same time, the spatial restrictions in built-up environments create their own challenges. Tightly packed facilities require mobile robots to be smaller and more agile. And while a comparatively cheap rolling platform with wheels suffices for a level surface, stairs present an insurmountable obstacle. So, if your inspection requires your robot to navigate irregular topography, you might be best served by Spot, the more expensive dog-like robot developed by Boston Dynamics.
But inspections are not always best served by grounded machinery. Drones are a popular alternative for equipment inspections, particularly in facilities with high ceilings that cannot be reached by robotic arms. However, the spinning blades that keep drones need unimpeded airflow from above, which means that ceilings can interfere with their flight pattern. It's key to take that into account because those blades can cause serious harm to workers and equipment.
Will your robots need to interact with workers?
Robots are meant to remove the risk of human error but deploying them improperly can make the consequences of mistakes even worse. As it stands, robots might need to work around workers, whose safety is paramount. That means that drones, for example, need to be encapsulated in rigid nets to prevent them from injuring workers if they malfunction.
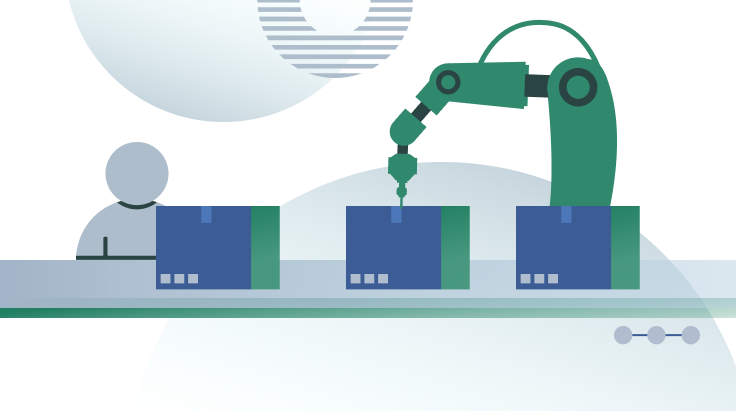
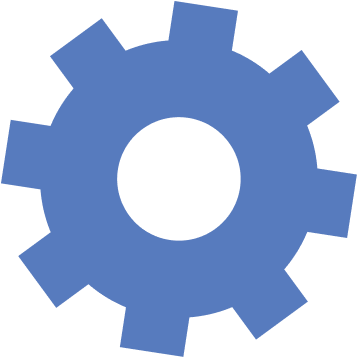
Full automation is the goal, but until then, worker safety is the key.
However, the safety netting itself can interfere with the drone’s flight path or prevent its sensors from working correctly. It also weighs the drone down, increasing its energy consumption and often requiring wiring or stronger batteries to maintain flight.
Those difficulties make robotic arms an attractive alternative to drones for inspections. However, non-collaborative arms need to be placed in cages to prevent them from injuring workers. Mobile robots are even required under EU law to have Light Detection and Ranging (LiDAR) sensors to avoid collisions. To ensure workers’ safety as you transition to full automation, it’s advantageous to consider using collaborative robots where possible.
Does your robot need to manipulate the object it’s inspecting?

Frequently, a robotic arm equipped with a camera and mounted on an axis serves to scan objects from multiple angles, generating a complete picture while using LiDAR to make sure that the arm doesn’t bump into the object. But if you want to view the object beneath, the arm might need to pick it up, running the risk of damage.
To avoid scratches and dents, the arm’s gripper will have to be fitted to the shape of the object itself, and the arm’s motors strong enough to lift it. Moreover, the robot will need to understand from which angle it can grasp the object and have the correct mechanics to not apply too much pressure.
And what if those objects are in motion? Production speed minimums prevent conveyor belts from halting, so making sure that sensors have adequate time may require your robot to move alongside the belt. And if you want to integrate your inspection with the production process itself, a pick-and-place arm must be able to transport the object to the next stage of production — while also inspecting it.
Some automated inspections will require more complex robotics than others, but one thing is always true: No automated inspection will be the same, and robotics is just one aspect.
Are you ready to figure out which automated visual inspection is right for you? SoftServe can help — let’s talk!