The Cost of Inaction
Unexpected equipment failures cost mining operations millions each year. Without predictive analytics and autonomous control, breakdowns continue to drain finances.
Traditional haul trucks waste 10-15% more fuel due to poor routing and idle times. This raises costs and harms the environment.
A shortage of skilled operators halts production. Companies face project delays or run below capacity. Relying on manual labor drives up recruitment and training costs.
Human-operated machinery causes 40-50% of mining accidents. Workers in hazardous environments face risks from machine injuries and fatigue-related errors.
You might think that modernization is risky, expensive, or only for industry giants. However, simulation-first approaches and automation are proven solutions grounded in real-world physics, high-fidelity modeling, and data. Modernization isn’t just for industry titans. Solutions like digital twins and simulation-first platforms are scalable, flexible, and, over the long term, cost-effective.
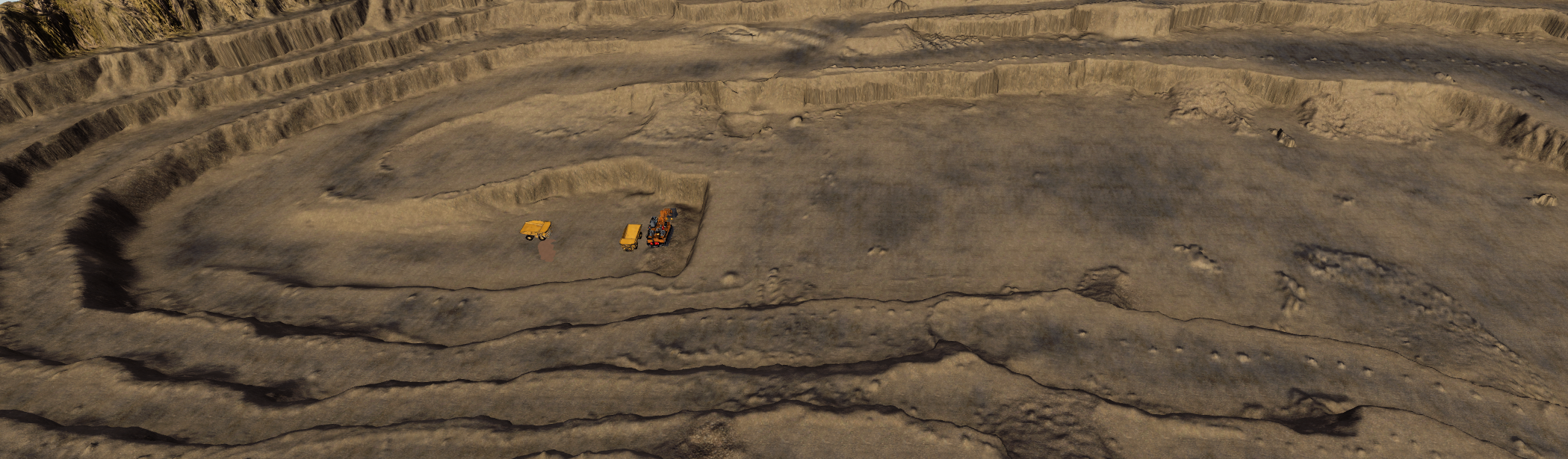
Benefits: Autonomous fleets and simulation-first
- Increase productivity and minimize downtime: Automated fleets run 24/7, increasing efficiency and reducing downtime from shift changes or fatigue.
- Lower fuel and energy costs: Autonomous navigation systems find the best routes in real-time, reducing idling and saving energy.
- Predict and prevent equipment failures: Realistic physical data from simulations provides the input for AI-powered diagnostics, enabling timely maintenance and extending equipment life.
- Test without risks: Digital twins mimic real-world conditions. They help companies improve autonomous control strategies and workflows before deployment. This ensures safer and more reliable automation.
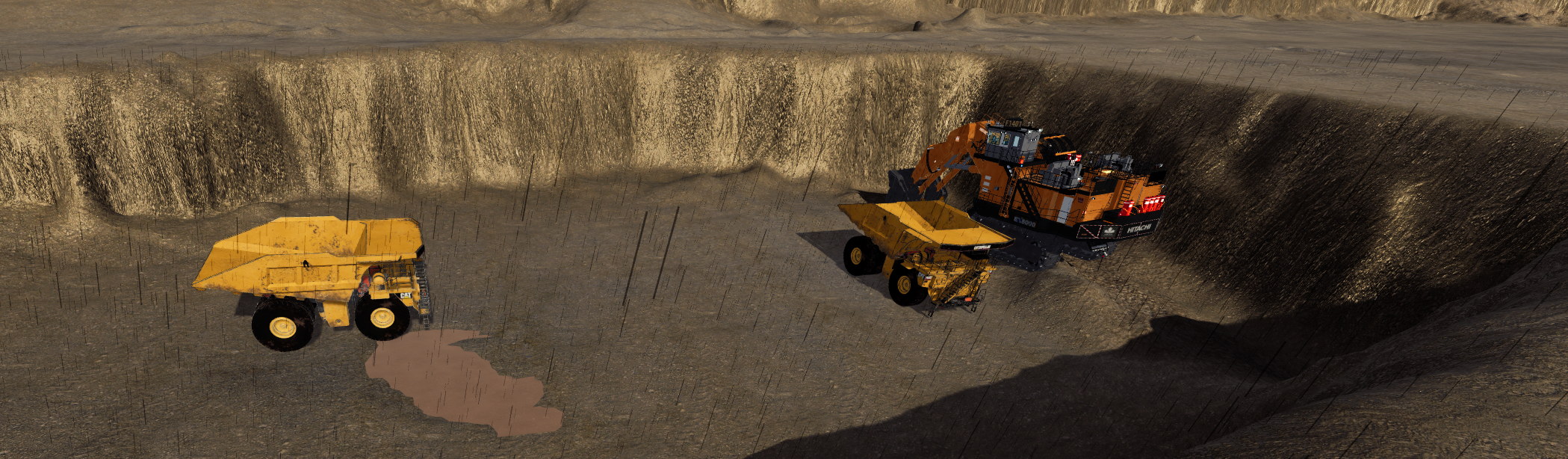
Features that deliver real ROI
- High-fidelity: SoftServe’s high-fidelity simulation integrates Algoryx’s physics engine with Unity-based visualization, ROS2-driven control, and the WARA-PS platform to create the ultimate testing ground for autonomous mining operations. With this setup, you can safely validate autonomous decision-making in a controlled environment, accurately modeling real-world conditions like terrain, soil behavior, excavation forces, and material interactions.
- Realistic visuals: Thanks to Unity’s HDRP rendering pipeline, the visuals are incredibly realistic—engineers can explore lifelike mine site simulations, test performance under different lighting and weather conditions, and fine-tune algorithms for better results.
- Advanced navigation: Beyond the visuals, our simulation-first approach ensures smooth control of autonomous vehicles, fleet coordination, and sensor-driven navigation. With tools like multi-modal SLAM and obstacle avoidance, vehicles can navigate tricky terrains, avoid hazards, and quickly adapt to changing environments.
- Scalable: What’s more, you can improve efficiency before rolling out automation in the field by analyzing energy use and managing loads in real time. Integrate various vehicle models to ensure the solution is scalable and adaptable for all kinds of mining operations.