Remote Support and Edge Device Management: Lessons From the Field
Over the years of working with industrial clients, I’ve seen operational efficiency evolve into the ultimate differentiator in a highly competitive landscape. One significant factor driving this efficiency is the increasing use of edge devices — compact, powerful computers placed close to processes and data origins. By processing data locally, these devices reduce latency, lower bandwidth usage, and support real-time decision-making right where it matters most.
While the benefits of edge computing are clear, they come with a new layer of complexity. Another crucial aspect to consider is the compelling need for a robust, reliable way to manage and support these devices remotely. Operating in locations like mines, offshore platforms, rural areas, or even on moving assets, these devices must remain online, secure, and regularly updated — even when network connections are spotty or fail entirely. In my experience working with clients, orchestrating thousands of these devices can be overwhelming without a comprehensive plan that factors in connectivity, security, and remote troubleshooting.
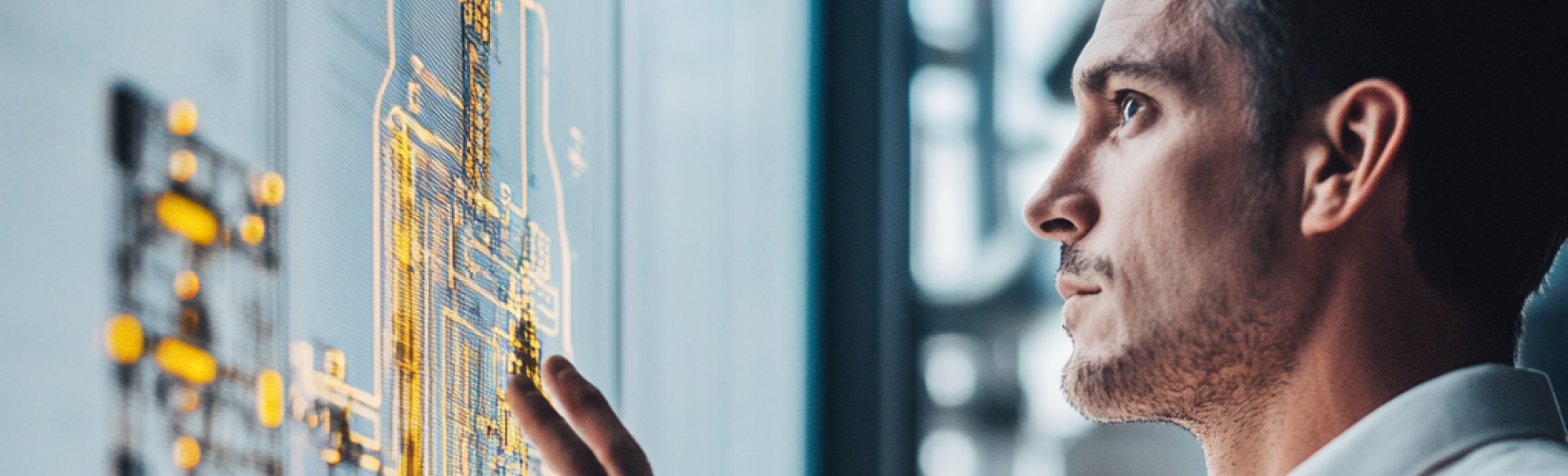
Why remote support matters
Remote support works in tandem with edge device management. It requires more than simply monitoring whether a device is on or offline; it’s about providing the ability to remotely diagnose, troubleshoot, patch, and even fix problems without physically dispatching a technician. When a device fails on an offshore platform or a remote pipeline site, on-site visits can be costly and time-consuming. By enabling remote support through robust, secure connectivity and device lifecycle management tools, organizations can reduce both downtime and operational costs while ensuring worker safety.
Several practical concerns emphasize the critical importance of remote support:
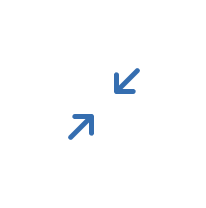
Reduced travel costs and risks: Sending field technicians to remote locations can involve helicopter rides, boat charters, or long overland trips. Remote support systems mitigate this by allowing experts to manage devices from centralized command centers.
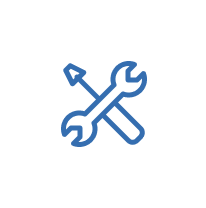
Faster mean time to repair (MTTR): Quickly diagnosing issues at the edge can prevent extensive downtime, ensuring production lines, drilling operations, or transport fleets don’t halt unnecessarily.
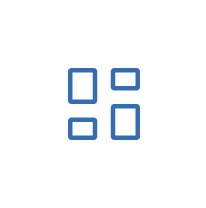
Scalable expertise: Through remote monitoring dashboards, fewer staff can supervise larger fleets of devices. This frees up resources for tasks that truly require in-person attention.
From buy vs. build to cooperative innovation
One question I often hear from clients is whether it’s better to build a custom solution for edge device management and remote support or to invest in an existing platform. The answer is rarely black-and-white.
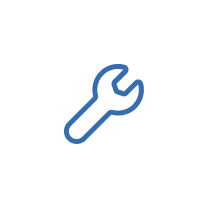
Building from scratch provides granular control but demands significant investment in specialized expertise, software development, and long-term maintenance.
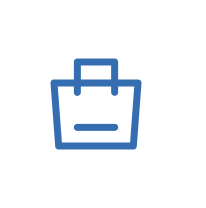
Buying or partnering with platforms like AWS IoT Greengrass, Microsoft Azure IoT Hub, or solutions from partners like Litmus offer faster deployment, robust security frameworks, and continuous feature updates.

Taking a hybrid approach by combining proven platforms with custom modules can achieve a middle ground — an optimal balance of reliability, security, and customization.
SoftServe’s holistic approach, supported by partners
At SoftServe, we adopt a holistic strategy for remote support and edge device management. Our partnerships with hyperscalers such as AWS, Microsoft Azure, Google Cloud, and platforms like Litmus enable us to create tailored solutions for each client. Whether the need is advanced analytics, secure connectivity, or AI-driven insights, we bring together off-the-shelf capabilities and custom components to meet specific operational requirements.
Challenges in managing and supporting industrial edge devices
- Connectivity issues. Efficient remote management depends on a reliable network, yet industrial settings — like mines or offshore platforms — have spotty connectivity. Our solutions use buffering, retry mechanisms, and remote diagnostics to maintain data integrity even when connections fail.
- Security issues. Edge devices hold valuable data and can become prime cyberattack targets if left unsecured. We advise using zero trust principles, robust encryption, and ongoing scans. By combining native security services from AWS, Azure, or Google Cloud with specialized tools (e.g., Litmus, SoftServe), companies reduce intrusion risks.
- Edge data processing. Industrial environments generate massive sensor or video data and sending it all to the cloud is often too slow or costly. Local analytics, enabled by platforms like Litmus and SoftServe’s EdgeInsight, handle time-critical processing on-site while the cloud focuses on storage and model training.
- Device lifecycle management. Over time, devices need patches, updates, and potentially decommissioning. Centralized processes ensure firmware and security remain up to date. By integrating AWS, Azure, or GCP with EdgeInsight, you maintain a unified fleet view — from onboarding to end-of-life.
- Remote troubleshooting and maintenance. Beyond monitoring, teams must quickly intervene from far away. Encrypted channels enable firmware updates, reconfigurations, or reboots without a site visit. In high-stakes industries, remote troubleshooting can reduce downtime from days to hours.
Industrial use cases
- Manufacturing: Real-time defect detection and predictive maintenance reduce downtime and keep quality high. In my personal experience, implementing AI-driven inspections on a production line can cut scrap rates by 50% or more.
- Energy and utilities: Remote wind farms rely on edge analytics to predict component failures and plan maintenance before catastrophic breakdowns occur. Remote support reduces the need for on-site technicians, especially in harsh weather conditions.
- Logistics and transportation: Vehicle health monitoring and cargo condition checks optimize routes and safety. Combining telematics with local analytics adopts real-time routing decisions that trim fuel costs and delivery times.
- Healthcare: Edge-based monitoring for hospital equipment and patient vitals yields quicker, more accurate response times, particularly in critical care.
Remote support in action: a quick example
Imagine a mining company running multiple edge devices in deep tunnels. During normal operation, these devices collect sensor data (temperature, humidity, air quality) and send it to the surface for real-time analytics. One device shows unusual spikes in temperature, potentially indicating a failing cooling system.
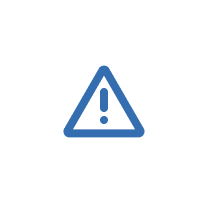
Alert and diagnosis: The central dashboard flags the issue, prompting a remote diagnostic session.
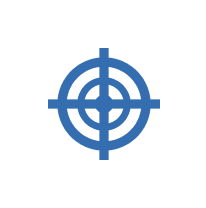
Remote troubleshooting: An engineer, located in a different city, logs into the device through secure channels. They review logs and run tests to confirm a fan malfunction.
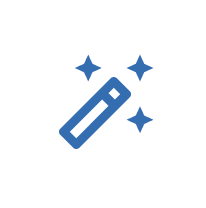
Rapid fix: The engineer pushes a firmware update that modifies fan speed parameters to manage heat better, buying time until a replacement fan can be physically installed. Production continues safely, and the client avoids major downtime.
Conclusion: why remote support and edge management are imperative
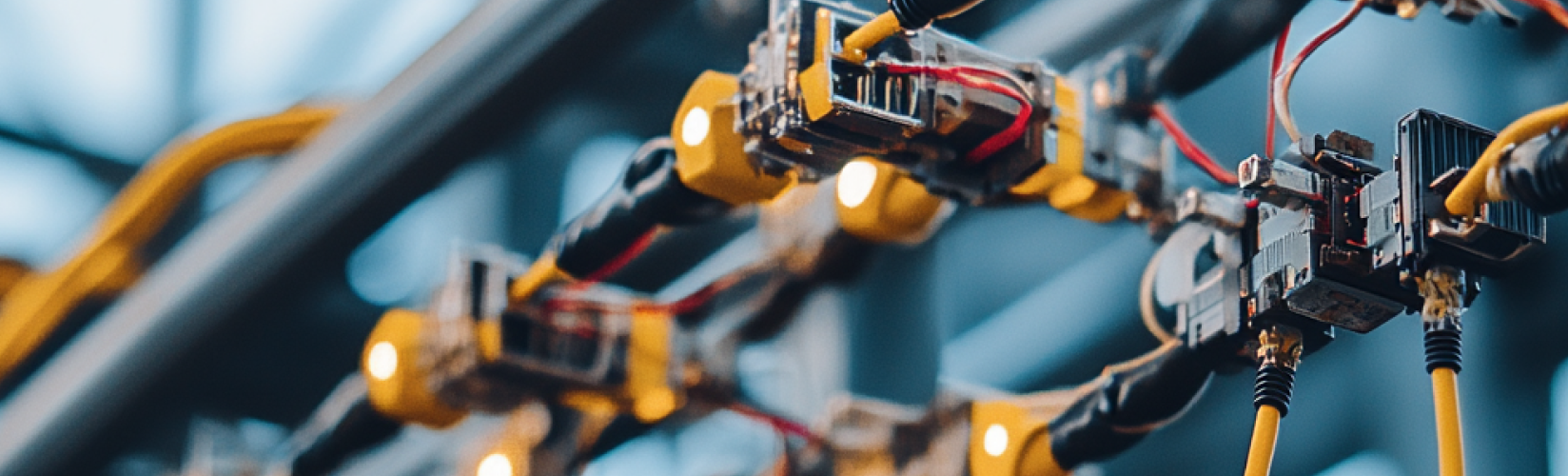
My takeaway from working with numerous industrial clients is that remote edge device management is no longer optional — it’s crucial for maintaining competitiveness and operational resilience. Whether you’re evaluating a buy-versus-build strategy or custom integrations, the real key is ensuring that your approach is flexible, secure, and designed to handle the scale of industrial operations.
By blending hyperscaler services from AWS, Microsoft Azure, and Google Cloud with specialized solutions like Litmus and SoftServe’s own EdgeInsight, organizations gain real-time insights, efficient remote support, and automated orchestration. This keeps devices running smoothly and equips teams with the data and remote-control capabilities they need to adapt quickly in a world where downtime costs can be immense.
If you’re ready to modernize your remote device management strategy or explore industrial AI at the edge, our teams at SoftServe are here to help. We can design a custom roadmap that aligns with your existing IT infrastructure, integrates seamlessly with your workflows, and delivers tangible outcomes — lower costs, boosted productivity, and safer, more reliable operations.
Let’s co-create a strategy that keeps your edge devices in peak condition, allowing you to focus on what truly matters: innovating and staying ahead in a rapidly evolving industrial landscape.
Start a conversation with us