Overall Equipment Effectiveness (OEE) is a powerful metric for improving manufacturing throughput. In fact, OEE is the first step toward driving meaningful advancements on the factory floor and a great place to start building more data-driven factory operations.
If you’re measuring OEE, even manually, that’s a great start. Chances are you've seen the benefits already, like improved equipment uptime, finding hidden performance issues, better resource allocation, and more accurate production targets.
Improving on OEE and taking it to the next level isn’t as daunting as you think. The overall improvements to factory floor throughput are well worth the time and investment.
The Three Steps
These steps are designed to be implemented on one machine for a more accurate OEE score, then replicated across all line equipment to improve production throughput.
Step 1: Automate Machine Data Capture
Manual data capture is prone to errors. Operators are hired to get your product out the door with speed and quality. Recording data is not their primary task. Most astute operators will jot down the basic data but shouldn't be the primary data source.
Manually inputting machine data is labor-intensive and only gives you a small percentage of the overall machine operations picture. It's usually too expensive to collect and correlate large data sets from various sources, rendering any meaningful analysis difficult.
Alternatively, let's say you're calculating OEE on a spreadsheet. If you automatically capture indexes like equipment uptime, speed, and performance, you’ll have definitively more accurate calculations.
We recommend you start automating machine data collection by connecting to machines running industrial protocols, like MQTT TCP/IP, OPC-UA 3, or Modbus RTU. Data capture interfaces already exist for these protocols. And for machines not running these protocols, you can start by using visual inspection, laser gates, or mechanical sensors to count the products going by.
Eventually, you'll want to invest in tools that will analyze the data and help you predict outcomes. That’s a more involved process and is the second phase towards improving manufacturing throughput.
Accurate real-time data automatically captured from machines creates the foundation for better OEE, and that will start driving continuous improvement.
Step 2: Implement a Simple Operator Reporting Interface
Even some of the most automated factories are a long way from zero human interaction. The people who operate the machines are the real engine of successful manufacturing operations.
You're probably thinking, "exactly, we can't completely take our operators out of the data collection process.” Agreed, you can’t.
Sometimes operators or quality control personnel need to stop operations abruptly. Other times, an engineer might notice a potential problem coming, or maybe the power goes out. When that happens, incident data on machines or operations need context.
For those times, create an application that makes it easier for engineers and quality control to fill in missing data. Provide specific questions and limited answer fields whenever possible. For instance, if someone hits the proverbial red button, the application asks,
“What happened?” and the limited list selections might be "breakdown," "power outage," etc. If the operator selects "breakdown," they are asked specific questions about the machine. If they hit "power outage," they might be asked, “is the outage specific to the factory?” or “is the outage area wide?”
Providing this type of interface will improve incident reporting, is less prone to errors, and more accurate, ultimately improving OEE.
Let's pause a minute before moving on to the next step. These two tasks alone will provide a marketable improvement in OEE, like spotting machine bottlenecks faster or more valuable reviews of unplanned downtimes.
The next step, however, will give you the roadmap to driving floor optimization by combining highly accurate machine data with production schedules.
Step 3: Integrate Your Machine Production Schedule Information
For this step, you're grabbing machine scheduling data, not all scheduling data. The data pulled into OEE is specific, like job sequence, production time to task, and employee resources schedule, making data automation manageable.
Automatically pulling the expected machine production rate and resource schedule data into OEE from either excel or your scheduling software program means a more accurate calculation of what was expected vs. what was produced. You're also comparing the production schedule data against very precise machine data.
The information is there to understand, by machine, the factory’s resources and how they should be utilized to streamline the production plan. More accurate machine data is used to produce better schedules and optimize time and resources, increasing your OEE score.
Automating data capture of your schedules and incorporating that data into your OEE also provides the foundation for creating a more dynamic scheduling of resources.
Conclusion
These three steps to a better OEE are just the beginning and will set your factory floor up for continuous improvement in production throughput.
Each step coincides with specific areas of OEE, giving you a better, more accurate view of factory floor operations. That's how we advise our manufacturing customers— to start with the basics and work towards continuous improvements, and each step leads to greater factory floor efficiency.
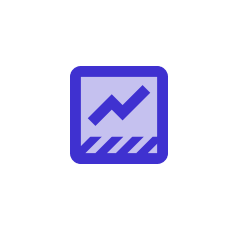
Equipment availability
Step 1: Automate Machine Data Capture
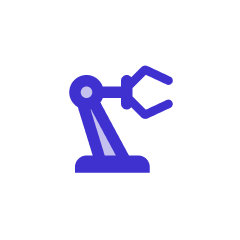
Equipment performance
Step 2: Implement a Simple Operator Reporting Interface
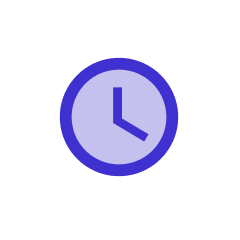
Efficient scheduling
Step 3: Integrate Your Machine Production Schedule Information
These three changes will vastly improve your OEE score and, in turn, manufacturing throughput.
Taking OEE to the next level means automating more data and adding rich context. How? By sharing data across your entire manufacturing ecosystem and linking up with ERP, MES, SCADA, CMMS, and other systems. To do this, you need to simplify your data collection process.
That's why SoftServe created the Production Data Tower. It's designed to simplify data collection and offers some game-changing benefits:
- Effortlessly run queries from your MES, SCADA, or ERP systems.
- Automate data collection with our adapters and connectors.
- Design data pipelines that keep your data flowing efficiently into our solution.
The best part? You can have the Production Data Tower up and running in minutes.