The Power of Simulation: Visibility and Compounding Efficiency
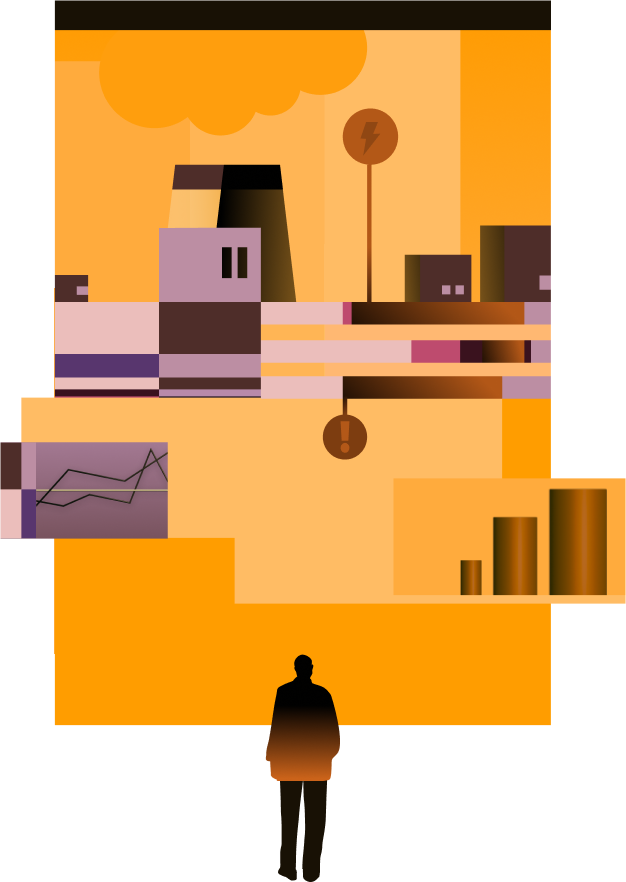
Monitoring can give you better visibility. Done right, it can position you for control over your entire production.
Monitoring is the first step to optimizing production, but many manufacturers lack the long-term vision to prepare themselves to reap its maximal ROI. As long as you continue to rely on expensive factory operators to carry out essential tasks manually, the risk of error will hinder your ability to move forward. By starting with a holistic approach—integrating data monitoring into a complete hardware-software automation stack—you can generate immediate returns while also creating a roadmap to robust data-based analysis and simulation. That can, in turn, set you up to maximize revenue and minimize costs on your investments.
Don’t settle for superficial visibility—leverage deep, data-based insights for maximal efficiency.
Monitoring in process manufacturing
Manufacturers are interested in monitoring for a variety of business reasons.
For example, when an industrial food producer began innovating in the vertical farm space, they encountered a hurdle. In order to make a vertical farm competitive with a traditional farm, it would have to be able to reduce its labor cost substantially.
The leafy greens grown in vertical farms must be plump yet crisp, bright green, and not too large to fetch the best price. Evaluation of each individual head is thus key to maximizing revenue. Because the manual inspection has high labor costs and is prone to human error, switching from manual to automated monitoring seemed like an intuitive first step to bringing costs down.
But does that go far enough?
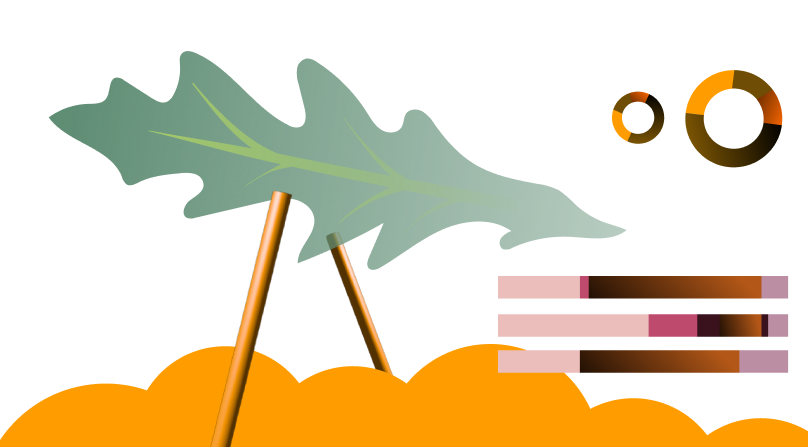
Visibility without control?
Monitoring can be—and should be—tied to the goal of process automation from the start.
The first reason is simple: If you have used automated monitoring to gain visibility into your operations but still rely on workers to act upon the insights, you’re still liable to suffer losses. Human error can corrupt the data provided by your monitoring technology—your investment won’t pay off as well as it could.

If you are interested in saving on labor costs while gaining deep data-based insights and enduring control over your production, you need to combine monitoring with the automation of production processes.
Thinking holistically about optimization
Our client began their collaboration with us to build a robotic solution to monitor the plants in an experimental vertical farm. But the price tag for the hardware nearly stopped the project in its tracks. To make the cost of the monitoring rig justifiable, our teams worked together to come up with a solution: We added the ability for the solution to automatically transplant seedlings after they had reached a certain stage of growth.
The solution was thus able to take on two manually performed tasks at once. Through daily measurements with 90% accuracy at €.01 per plant per life span, our client gained greater insights at a lower price than manual operators could ever provide. And thanks to being tied to process automation, our client unlocked several other opportunities:
![]() Integrated growth process by tying monitoring to transplanting |
![]() More reliable database through auditable production processes |
![]() Complete simulation of every individual plant for revenue maximization |
Beyond marginally boosting visibility and reducing labor costs, our client gained the ability to optimize their entire production process.
Compounding efficiency
By combining automated monitoring with automated processes, you can create a virtuous cycle. Automation gives you a stronger data foundation; you can then analyze your automation with that data. In the end, you will gain the ability to simulate aspects of your production, taking you one step further to production optimization.
Our client leveraged this capability to begin automating the monitoring of more aspects of the growth cycle and further production steps.

Most importantly, they started using the simulations to implement a data-based energy optimization project.
But their project didn’t end there—if you want to learn more about what we did for our client, check out the case study here.
And if you are interested in setting yourself for compounding gains and fast ROI, let’s talk.